Custom Designed Grinding Systems
Systems for Special Applications

A custom designed CNC grinder for grinding parts in a coil. Two stations with separate CNC controls coordinate the grinding between two different types of grinding. This was a five axis special design for a customer's unusual requirement. NEMT provides custom and special designs from the ground up.
Custom designed 4 axis CNC grinding wheel profiler with two grinding spindles finishes profiling of complex wheel forms in one operation. One spindle trues and sizes the wheel OD. A second spindle with a programmable tilt creates a thread form in the grinding wheel. The profiling uses four synchronized axes to generate the profile. The system uses a dual path Fanuc control with NEMT custom software


Custom designed 6 axis, dual head CNC grinder with robot loading. This CNC grinder was designed to eliminate loading time for medical devices. It features two workheads and two grinding fixtures. While the grinding spindle is grinding the part on one head, a robot is loading the fixture on the second head. Grind to grind time is less than two seconds. The robot picks up the medical device from a magazine in the rear of the grinder and puts it into a cassette for transport to the next operation.
Hopper fed CNC grinder with two spindles produces a part every 10 seconds. A special design hopper feed lifts shafts from a queue and automatically loads it into a special fixture for grinding. This totally custom grinder was developed in our 3D CAD system

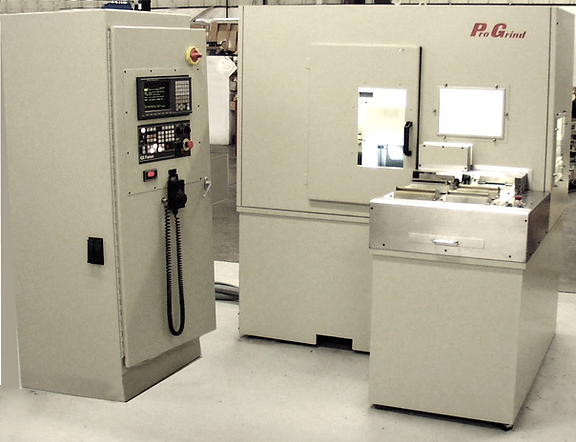
3 Axis CNC ceramic grinder with 20 wheels and automatic pallet loading. This custom design grinder was built to slice ceramic billets. It features an automatic pallet handling system. Because coolant could not be used, a special system was developed to control dust and remove it from the grinder.